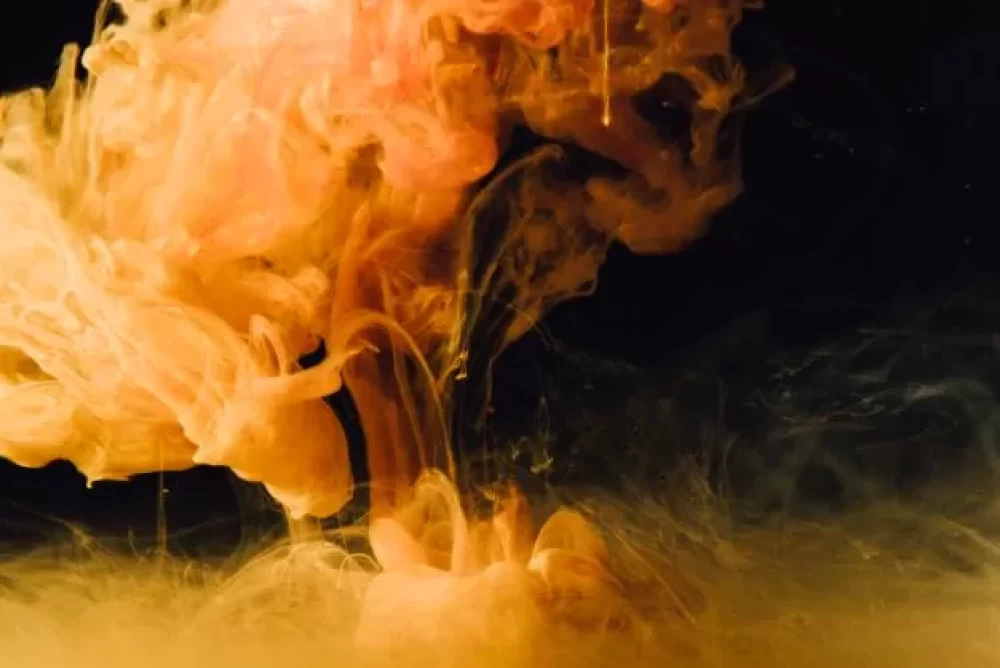
Downloads
This section is designed to provide you with easy access to valuable materials that you can view and download at your convenience. Here, you’ll find a diverse range of resources that you can easily view and download. Remember, new materials are added regularly, so be sure to check back often to stay up-to-date with the latest resources
-
FileType
-
1500i - Data SheetProducts
-
1750i - Data SheetProducts
-
1750i PVC - Data SheetProducts
-
200 - Data SheetProducts
-
2000i - Data SheetProducts
-
200i - Data SheetProducts
-
200i HP - Data SheetProducts
-
2Tip - Data SheetProducts
-
3-15 Tip - Data SheetProducts
-
300i - Data SheetProducts
-
400 - Data SheetProducts
-
400i - Data SheetProducts
-
400i Dye Sub - Data SheetProducts
-
400i Ozone - Data SheetProducts
-
400i PVC - Data SheetProducts
-
5000i - Data SheetProducts
-
5000i HD - Data SheetProducts
-
5000i PVC - Data SheetProducts
-
650 - Data SheetProducts
-
750i 2 Tier - Data SheetProducts
-
750i 3 Tier - Data SheetProducts
-
800 - Data SheetProducts
-
800i 2 Tier - Data SheetProducts
-
800i 3 Tier - Data SheetProducts
-
800i PVC - Data SheetProducts
-
Alpha 400 - Data SheetProducts
-
Arm Kits - Data SheetAccessories
-
Cascade Filter - Data SheetAccessories
-
Compressor - Data SheetAccessories
-
Connection Kits - Data SheetAccessories
-
CUB3D - Data SheetProducts
-
Cyclone - Data SheetAccessories
-
Ebase - Data SheetProducts
-
Enclosure - Data SheetAccessories
-
FumeBuster - Data SheetProducts
-
FumeCube - Data SheetProducts
-
FumeCube Dust - Data SheetProducts
-
FumeCube Lite - Data SheetProducts
-
FumeCube Max - Data SheetProducts
-
FumeCube Pro - Data SheetProducts
-
Hose Length - DatasheetAccessories
-
iFume 400i Green - Data SheetProducts
-
iFume 400i Orange - Data SheetProducts
-
iFume 400i Ozone - Data SheetProducts
-
iFume 400i PVC - Data SheetProducts
-
iFume 400i Red - Data SheetProducts
-
iFume 400i Violet - Data SheetProducts
-
Inline Carbon Box - Data sheetAccessories
-
Interface GuideAccessories
-
LaserSafe - Data SheetProducts
-
Oskar Arms - Data SheetAccessories
-
Pad Filter Box - Data SheetAccessories
-
PUR35 - Data SheetProducts
-
PUR35 Chemical - Data SheetProducts
-
Purex Pulse Jet- Data SheetProducts
-
Reducers - Data SheetAccessories
-
Spark Arrestors - Data SheetAccessories
-
Vent To Air Exhaust Cowls - Data SheetAccessories
-
Weldex - Data SheetProducts
-
XBase - Data SheetProducts